EVA Bags
Low Melt EVA Bags: The Smart Solution for Safe, Seamless Packaging
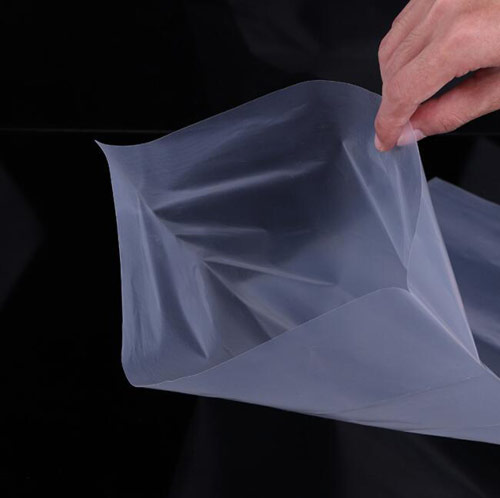
At Premier Greentech, we are proud to be a leading manufacturer and supplier of Low Melt EVA Bags, designed to revolutionize the rubber compounding and polymer processing industries. Our Batch Inclusion EVA Bags are crafted using the highest quality EVA resins and advanced manufacturing techniques to ensure precision, efficiency, and safety in every production process. Trusted by industries worldwide, our EVA Bags offer a smarter, cleaner, and more efficient solution for handling and delivering additives in rubber and tyre manufacturing. Whether you need improved batch uniformity, contamination-free mixing, or enhanced workplace safety, Premier Greentech's EVA Bags are the trusted choice for performance and reliability.
EVA Bags: Smart Packaging for Smarter Compounding
At the intersection of innovation and precision, our Low Melt EVA Bags-also known as Batch Inclusion Bags-are revolutionizing the way industries handle raw materials in rubber compounding and polymer processing. With cutting-edge technology and premium-grade EVA resins, these bags ensure clean, accurate, and efficient ingredient handling during the compounding process.
What Sets Our EVA Bags Apart?
Crafted with state-of-the-art manufacturing techniques, our Low Melt EVA Bags are the result of rigorous research & development, strict quality controls, and a deep understanding of industrial needs. Every bag is produced to meet and exceed global industry standards, making it a trusted solution across a wide range of applications-from rubber and tyre manufacturing to polymer processing.
What is a Low Melting EVA Bag?
A Low Melting EVA Bag, also called a Batch Inclusion Bag, is a specially designed packaging solution made from Ethylene Vinyl Acetate (EVA)-a flexible and low-melting-point plastic. Primarily used in tyre manufacturing, rubber compounding, and polymer processing, these bags deliver chemical additives directly into mixing systems like Banbury or internal mixers.
These bags are designed for pre-weighing and delivering rubber chemicals, playing a critical role in ensuring precise and contamination-free addition of ingredients. They are tailored to accommodate various rubber chemicals, making them indispensable for modern compound preparation.
Designed for High-Heat Environments
Internal mixers typically operate at temperatures above 120°C, but our EVA bags are engineered to melt completely at around 80°C, ensuring the bag dissolves quickly and safely. This process ensures the contents are uniformly released into the rubber compound without leaving behind any residue, improving product consistency and quality.
Compatibility & Performance
- Highly Compatible: EVA Bags are perfectly compatible with all rubber compound ingredients, ensuring seamless integration into the mix.
- Zero Residue: When melted, the bags become a part of the rubber compound, even contributing to the total weight of the compound.
- Enhanced Batch Uniformity: By eliminating the need for manual handling of powders, EVA Bags improve batch consistency and significantly enhance safety during production.
Smart Material, Smarter Production
Manufactured from ultra-thin yet durable EVA film, these bags are tough enough to handle packaging, transport, and dosing, yet delicate enough to melt instantly under heat. This makes them ideal for cleanroom operations and automated production lines where hygiene and efficiency are paramount.
How It Works
Instead of manually adding powders or liquids into mixers-often a messy and hazardous process-our Low Melt EVA Bags offer a smarter solution. The ingredients are pre-packed into the bags, which are then dropped directly into the high-temperature internal mixer. As the bag melts, it becomes part of the final product, without affecting the mix quality or composition.
Eco-Conscious & Efficient
Not only do Low Melt EVA Bags save time and reduce material waste, but they also contribute to a cleaner and safer production floor. By minimizing direct contact with potentially hazardous powders and eliminating spillage, these bags support eco-conscious operations and promote better health and safety standards for workers.
Your Trusted Partner in Process Innovation
Whether you're in the tyre, automotive, footwear, or general rubber industries, Premier Greentech's Low Melt EVA Bags offer a next-generation packaging solution. They enhance consistency, improve safety, and optimize your production cycle. With our unwavering commitment to quality and innovation, we provide packaging solutions that are not only efficient but also smart, safe, and future-ready.
Key Characteristics
- Melting Point: Typically melts between 70°C to 110°C, depending on formulation.
- Made From: High-grade EVA (Ethylene Vinyl Acetate) resins.
- Purpose: Eliminates the need for manual handling of additives, improves batch accuracy, and promotes a cleaner working environment.
Benefits
- Clean & Dust-Free Operation
- Accurate Ingredient Dispersion
- Improved Worker Safety
- Faster Production Cycles
- No Residue or Contamination
- Environmentally Friendly
Where It's Used
- Tyre manufacturing
- Rubber compound mixing
- Automotive rubber parts
- Conveyor belts and industrial rubber goods
- EVA foam products
- Footwear manufacturing
Key Features
Our Low Melt EVA Bags are designed with precision and performance in mind, offering a reliable solution for clean, safe, and efficient handling of rubber chemicals and additives.
- Tear-Resistant : Withstands handling and packaging without compromising integrity
- Heat Resistant : Maintains structural integrity up to the melting point
- Dimensional Accuracy : Precisely cut and sealed for consistent weight and size control
- Low Melting Point : Melts completely at 70°C to 110°C, allowing seamless integration into rubber compounds without leaving any residue or affecting the mix quality.
- High Compatibility : Formulated using chemically inert EVA resins, these bags are fully compatible with all rubber compound ingredients and become part of the final product.
- Excellent Dispensing Ability : Engineered for smooth material release, the bags prevent clumping or sticking, ensuring accurate and consistent dosing into the mixer.
- High-Quality EVA Resins : Manufactured from premium-grade resins, these bags ensure durability, uniformity, and process safety across every batch.
- Cleanroom-Friendly : Perfect for environments that demand hygiene and dust control, EVA bags help maintain a contamination-free workspace, improving both safety and product quality.
Specifications of EVA Bags (Batch Inclusion Bags)
Our Low Melt EVA Bags are available in a variety of grades and customizable sizes to suit the specific requirements of rubber and polymer processing industries. These bags are engineered for complete melt-inclusion during mixing, offering excellent chemical compatibility and thermal performance.
- EVA BAG-65 DSC SP 65-70 Degree Celsius
- EVA BAG-80 DSC SP 80-85 degree Celsius
- EVA BAG-100 DSC SP 100-110 degree Celsius
- Width - 6"-90"
- Length- As per requirement
- Thickness - 25 micron to 150 micron
- Color - Natural, Red, Blue, Green, Yellow, Brown, Pink, Orange
Applications of EVA Bags
Our Low Melt EVA Bags are widely used in:
- Tyre Manufacturing : For direct batch addition of carbon black, sulfur, accelerators, and process oils in internal mixers.
- Rubber Compounding : Ensures precision dosing and uniform distribution of additives for technical rubber goods.
- Footwear Industry : Streamlines sole and midsole manufacturing in EVA and rubber-based shoes.
- Automotive Rubber Parts : Perfect for controlled inclusion of curatives and fillers in engine mounts, gaskets, and more.
- Industrial Belting & Hoses : Ensures safe and efficient processing of heavy-duty rubber-based components.
Global Export of Low Melting Eva Bags
At Premier Greentech, we are proud to be a leading manufacturer and supplier of Low Melting EVA Bags, trusted by industries worldwide for their efficiency, precision, and environmental benefits. Our EVA Batch Inclusion Bags are revolutionizing the way rubber and chemical additives are handled during the mixing process-melting seamlessly into the compound and eliminating waste, contamination, and cleanup hassles.
With a strong global footprint, Premier Greentech exports its high-quality EVA Bags to several countries across the world, including the United States, Canada, United Kingdom, Germany, Australia, South Africa, United Arab Emirates, Saudi Arabia, Qatar, Kuwait, Indonesia, Malaysia, and Vietnam.
Our commitment to international standards, advanced manufacturing, and customer satisfaction has made us a trusted name across diverse industries, from rubber compounding to tyre production and polymer processing.
When you choose Premier Greentech, you're choosing innovation that travels far and wide-delivering quality, reliability, and performance at every step.
About Other Products
Premier Greentech is a trusted manufacturer and supplier of high-performance tapes and packaging solutions. Our product range includes Barricading Tape, ideal for cordoning off hazardous areas, Anti Skid Tape for enhancing floor safety, and Floor Marking Tape to organize and optimize workspace layouts. We also offer durable Plastic Packing Material for secure packaging, along with Hot Melt Adhesive Film that provides strong, reliable bonding across various applications. For increased visibility and safety, our Reflective Tape is the perfect choice for both indoor and outdoor use.